🔍 > Lean Terms Directory |
Walk Time
Walk time is an important factor in continuous improvement. Its main impact is on the seven wastes and on Standard Work. Obviously, the problem is that walking takes time that could be better spent working on a process. Walking distance adds up in a surprising hurry.
For example, if a person walks just 50 feet during a process, he or she does 30 times a day, it adds up to 1,500 feet per day, or 1.4 miles per week. Assuming 50 work weeks in a year, and that turns out to be 71 miles. At 3 mph, 50 feet translates to nearly 24 hours of walking in a year. And when the distances or cycles rise, the time increases rapidly.
In one case where I was helping a team improve a process, there was a copier located across a hallway. They walked across that hall so frequently over the years, a groove had been worn into the tiles on the floor. It takes a lot of time to walk back and forth over a hard surface enough to create a groove that was deep enough to hold water. And remember, that time was paid time. The cost of a second copier was miniscule compared to paying highly skilled, highly compensated technicians to walk back and forth across a hallway.
While not explicitly a category of waste, walk time is a component of both transportation and motion. Transportation involves the movement of parts, materials or tools. In addition to hand movements, many people place walking empty-handed in the motion category. However, you choose to categorize it, though, the further one has to walk, the longer a process takes.
Walk time is also shown on a standard work combination sheet. It is depicted as a squiggly line joining the horizontal lines representing tasks. The most common form of walk time in standard work is when an operator has to go back to the start point for the process after completing a cycle.
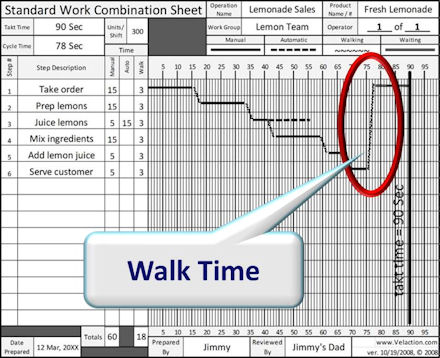
“Walk Time” as depicted on a Standard Work Combination Sheet
Walk time is reduced through a variety of methods. Creating functional cells where process steps are co-located and reducing the size of the cell’s footprint both limit distances. One common way of reducing the work area is to eliminate inventory. Fewer items means less storage space and that translates to less walking. U-shaped cells are a common solution to the problem of walking back to the start point.
0 Comments