> Continuous Improvement Articles
The Perception of Activity
We want people to stay busy, right? Idle people are wasteful, right?
In Lean, these are both false.
I would rather see a person sit idle than just try to fill the time with busy work. Busy work masks opportunity. It is understandable that people do this. If they sit still, typically two things happen.
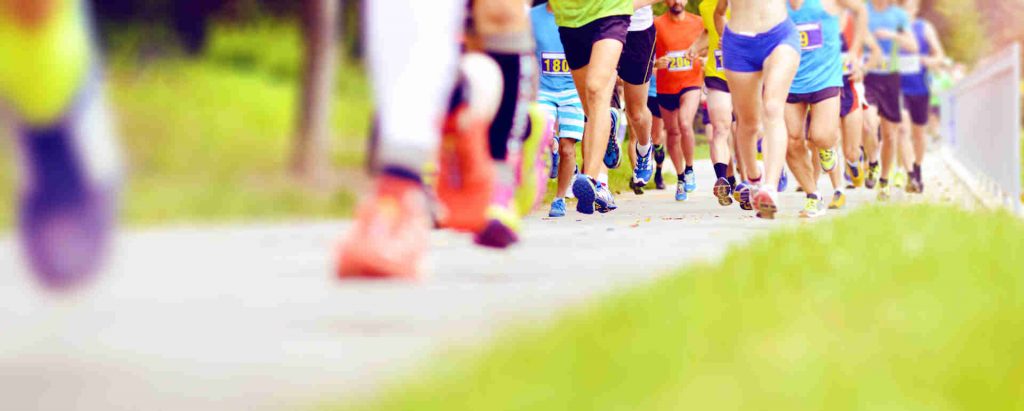
The first is that their boss comes over and chews them out for sitting around. We’ll talk more about who really is at fault here in a minute…
The second is that they know that sitting around will get more work piled up on them.
Let’s look at the first event. An operator finishes up her job early, and then chills out. Maybe gets a drink, or zips off a quick text. The boss sees and comes over to chastise the employee. Remember—this employee did everything she was asked to do, and did it well, and on time.
But now, she’s being trained to look busy. To string work out so she won’t get in trouble. That’s not really what the manager really wants.
Which leads us to the second event. Let’s say that the manager is a somewhat Lean thinker and realizes that the idle time is an invitation to balance the line better. He sees our diligent worker standing around fairly often, so adds some more tasks to her standard work. He expects to see everything hum along, but instead the worker is now behind a lot, and is constantly pulling the andon cord.
What happened? Variation happened. Our worker doesn’t have free time every cycle. There might be a problem with defects. Bad parts might affect every 6th or 7th line shift. It might be options on the products she is building. The base model is easy to build, but the ‘Widgetizer’ add-on option pushes her over the limit.
Our proactive worker won’t let this mistake happen again. She’s going to operate as if things were worst case every time. With poor leadership, it’s a no-win situation. Either the operator looks idle and accepts the stigma that goes with that, or lets the work expand to fill the time available so she doesn’t cause problems when the variations, planned or unplanned, happen.
So, what is a Lean leader to do?
The first thing is to be clear about what the standard is. That means real standard work. And it means tracking variations. The key is to really understand processes and know how long tasks should take. Whenever something out of the ordinary happens, it should be noted so the team can understand where the biggest sources of problems are.
The next thing to do is to really make it clear that people should not just do busy work when they finish their tasks. That’s not to say they can’t be assigned a subset of tasks that aren’t so time critical. They could do those whenever things work as planned. Refilling materials, emptying trash cans for the team, etc.
They could also man a feeder line and keep a component in stock. For example, they could build limit switch assemblies. Do this with a kanban so production isn’t out of control. The key is to be structured.
Leaders should also rotate people to different jobs. Some jobs will get the reputation for being easy or hard. Share the ups and the downs. Job rotation also acts to shed light on how long processes really take.
Now, this article has focused on the shop floor, but the concepts are the same in the office. In fact, the idea of looking busy is even more pronounced in the office. People are a lot more protective of their time, as the demand fluctuates much more and work doesn’t keep. They know if they don’t look busy, they will get more work, and that will bury them on the next demand uptick.
Leaders can use daily management to predict the workload and staff appropriately. The key is to have a clear understanding of the workload—a reasonable workload—so that people don’t feel the need to game the system.
The bottom line is that managers have to walk the talk about busy work. They can’t even give the impression that looking busy is important. Rather, managers need to make sure that people have productive work to do when the are done with their standard work. And they have to make sure that team members have help when they need it so the extra work assigned to fill the voids doesn’t become overbearing.
0 Comments