> Continuous Improvement Articles
Standardization: Process Enhancer or Creativity Killer?
Back in May, I was a guest author on Ron Pereira’s LSSAcademy blog. (Click this link for the article on Leadership and Standard Work)
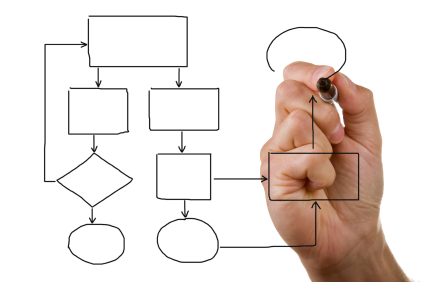
Does Standardization Reduce Flexibility of a Process?
Well, I went back today to see the comments, and saw one that got me thinking. The commenter questioned the application of the standardization process to the problem solving methodology.
The quote was:
I find such dogmatism in the name of standardization stifling.
It got me thinking. This is one of the many challenges people in Lean office settings face. They want flexibility in how they do their process, and perceive standardization as a barrier to autonomy.
Process Standardization Happens All Around Us
I’ve always wondered about that. We don’t see the standard practice of driving on the right side of the road stifling. We don’t perceive assigning a single phone number to a single phone as a barrier to thought. We like having prices marked on the items we buy at the store—we don’t think that it is disrespectful to the clerk to have to ring the same item up the same way for everyone.
My point is that we are accustomed to standardization in our daily lives, and it provides a measure of smoothness and efficiency, and even safety as we go about our business.
Process Standardization Causes Struggles in the Lean Office
Even so, standardization is one of the bigger obstacles that frontline employees and professionals face in administrative processes as their company moves Lean into the office. They perceive that standardization kills creativity.
As a counterpoint to that though, I offer two words that have arguably been responsible for some of the greatest creative gains of our time: Scientific Method. Isn’t that just a standardized process for thinking?
Standardization is not the problem. It’s change. It is the perception that something is being taken away. So, Lean should give something in return. It should give frontline employees the authority to change processes that are not working. When employees see that Lean is working for them, they will be more likely to support, or even embrace it.
Special Bonus Point Section: Anyone who noticed that the process flowchart in the stock photo I used doesn’t have a start point gets a big pat on the back!
0 Comments