🔍 > Lean Terms Directory |
Setup Reduction
Setup reduction is the act of lowering the time it takes to switch from one product to another.
In a traditional manufacturer, the switching time (changeover) is long. As a result, if they do more than an occasional switch, they run out of production time. So, they produce long runs of parts, adding to inventory and all the problems that brings: more space for storage, more quality problems, more money tied up in inventory, more inventory management, longer lead times, etc.
On the other hand, it follows that if the company could cut setup time in half, they could do twice as many product changes without taking away any more production time. That would let the company produce fewer parts at a time, as they would be able to cycle through all the parts in half the time.
In this image, setup time takes two hours. The whole day is then spent producing the same part.
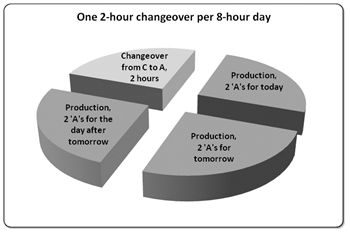
Prior to Setup Reduction
Without setup reduction, if you tried to run every part every day, you’d only be able to do a portion of each product.
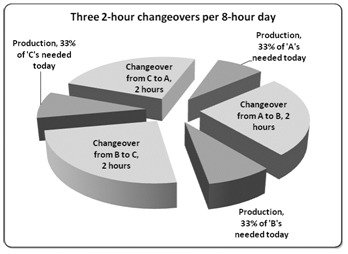
Too Many Changeovers
If you were able to reduce the setup time, though, you could run a day’s worth of each product every day.
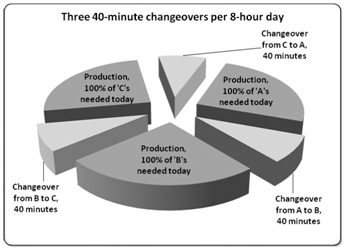
Setup Reduction Equals Smaller Lots
It follows that more setup reduction will further reduce how long it takes to cycle through all the parts.
Setup reduction is arguably the tool that hast the greatest enabling effect on Lean. It allows companies to reduce inventory and all its associated waste. It speeds up the lead time and makes the company more flexible when demand shifts.
Without an aggressive effort to reduce changeovers and lower the amount of inventory, flow is difficult, if not impossible to achieve.
0 Comments