> Continuous Improvement Articles
How to 5S. Or More Accurately, How NOT to 5S.
5S is one of the building blocks of Lean, and really, any continuous improvement effort. Learning how to 5S properly can launch a company on the path to greatness. Unfortunately, many companies don’t learn how not to 5S. What you don’t do can be as important as what you do.
How NOT to 5S
When I was at West Point, we had to make our beds in precise military fashion.
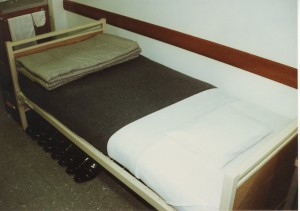
An Example of How NOT to 5S
There was a purpose to it. It was intended to instill discipline and uniformity in an organization that relies upon cohesion to function properly.
But despite the organized, neat appearance, this is not a lesson in how to 5S. In fact, it was about as far from solid 5S practices as you could have.
Every night, all the cadets would throw a spare sheet on top of the made bed, unfold their comforter, and sleep without ever disturbing the neat hospital corners. In the morning, we just folded the comforter, pulled our blankets tight, and went about our day.
Think of all the waste there would be if this was a production environment. But similar wasteful 5S activities happen all the time when people don’t know how to 5S with a purpose.
All 5S activities should reduce waste, not create it. For example, labeling a location for a stapler in a shared printer area helps quickly identify when it is missing. But there’s no point in labeling the location for a coffee maker. I’ve never seen a person move the machine out of an area, or misplace it. Spending the time and money on labeling static items doesn’t add value.
Think through how your 5S activities will improve your process before you spend any resources on 5S with no purpose.
0 Comments